As the demand for both commercial and military aircraft increased dramatically over the past several decades, manufacturers sought out the use of new production partners, new manufacturing techniques, and new materials. The intent was to stimulate product and production research and development while sharing the potential risk and reward spread over an increased number of partners. The goals were to gain economies of scale, improve the manufacturability without proportionately increasing labor costs, and increase production rates, while lessening lead times.
The Concept of Simulating Assembly
The concept worked well by stimulating creativity in new materials and manufacturing techniques. Centers of excellence were developed through worldwide partnerships that focused on specific components or manufacturing challenges. Though similar efforts had always been in use, this new effort focused on building complete components ready for final assembly. The use of new composite materials expanded rapidly resulting in reduced weight (gaining fuel economy) and the potential for long term reduction of production costs.
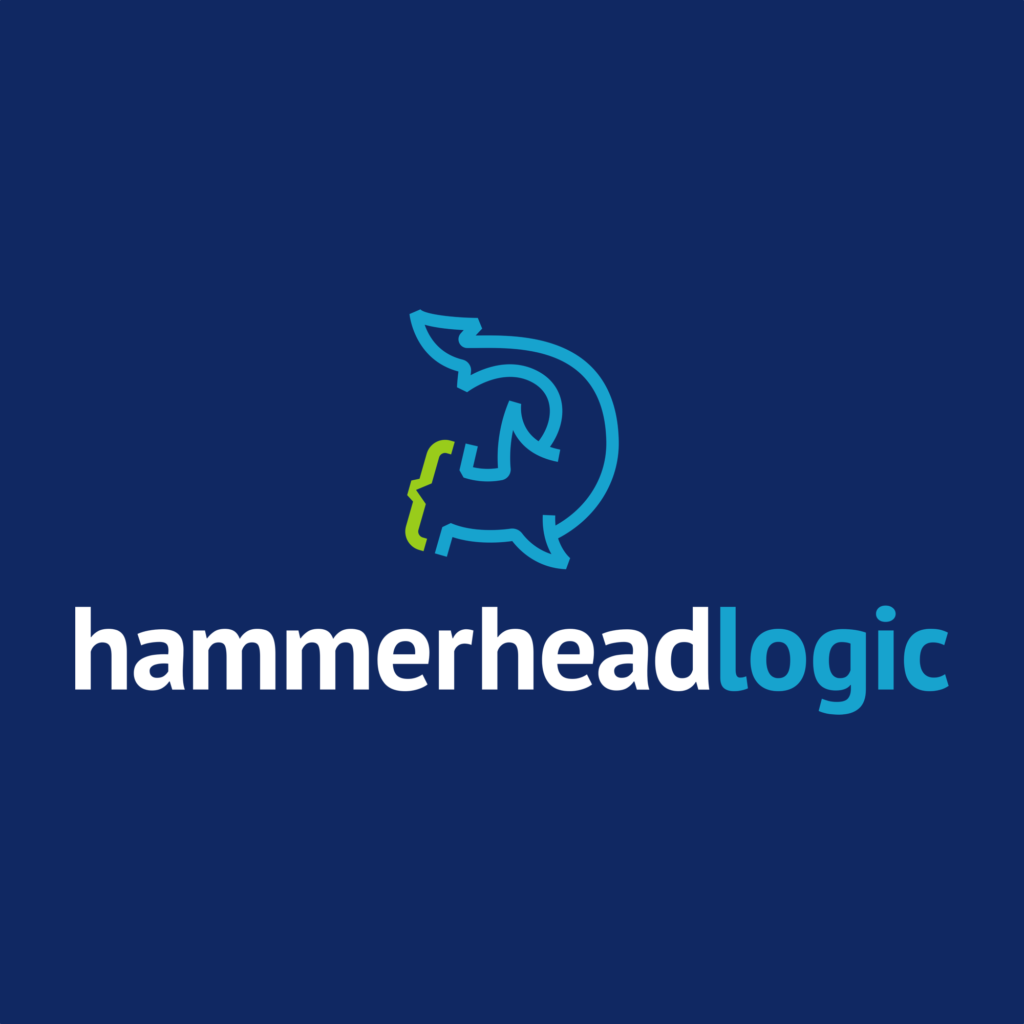
As production rates increased, major components were completed by local partners before shipping to centralized final assembly halls. Aircraft manufacturers began to realize a byproduct of producing and then shipping these new engineered components was increased product variance.
Our Software Solution
The HammerHead Logic team developed a solution to capture the “as built” condition of all major components, such as fuselage, wings, and tail section prior to shipping. Each component was digitized using cutting-edge, large-scale measurement sensors. By using graphical part simulations (supported by high degree of mathematical precision), the types of sensors, quantity, position, and orientation could be simulated and then optimized to achieve the best digital model of each part.
These digital “as built” models were then used to simulate, visualize, and optimize the joining of major components. Using the optimized simulation, the actual join process is planned and then completed using external digital monitor systems (some capable of six degrees of freedom monitoring) to guide the actual part mating. Once in full use, components were usable before shipping, which reduced non-conforming components and receiving inspections. The final assembly plan was assured to be successful.
Versions of this application are in use by major commercial airline manufacturers worldwide and the same systems are in use with spacecraft, rotorcraft, ships, and a variety of military air vehicles. In each solution, time for final assembly was dramatically reduced and production rates increased.
Let’s Talk About Digital Assembly
Our approach to digital assembly can be applied to many industries. The use of best fit algorithms, applied numerical optimizations, spatial transformations, and spatial relationships can be useful in solving a wide variety of manufacturing challenges. If you have a unique problem that needs a fresh solution, let’s talk about how we can help.